
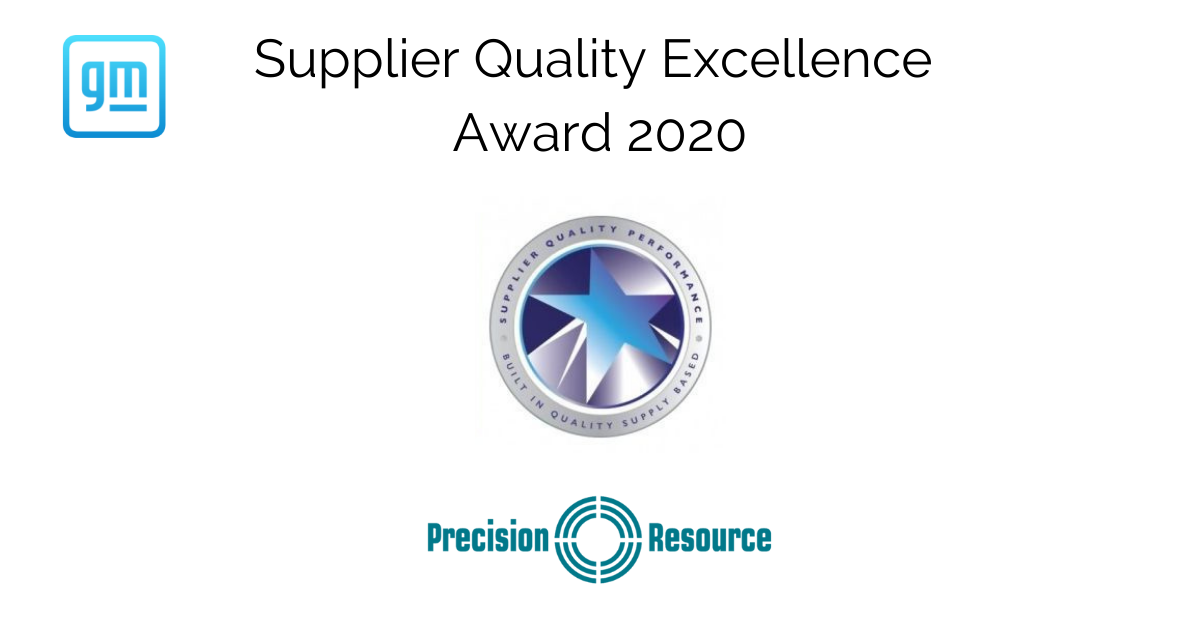
“We contact the suppliers to be sure they are healthy and safe. From there, the process is straightforward. Quickly convening a crisis room, the five-person team used GIS-based maps to identify suppliers within a 100-mile radius of the quake.
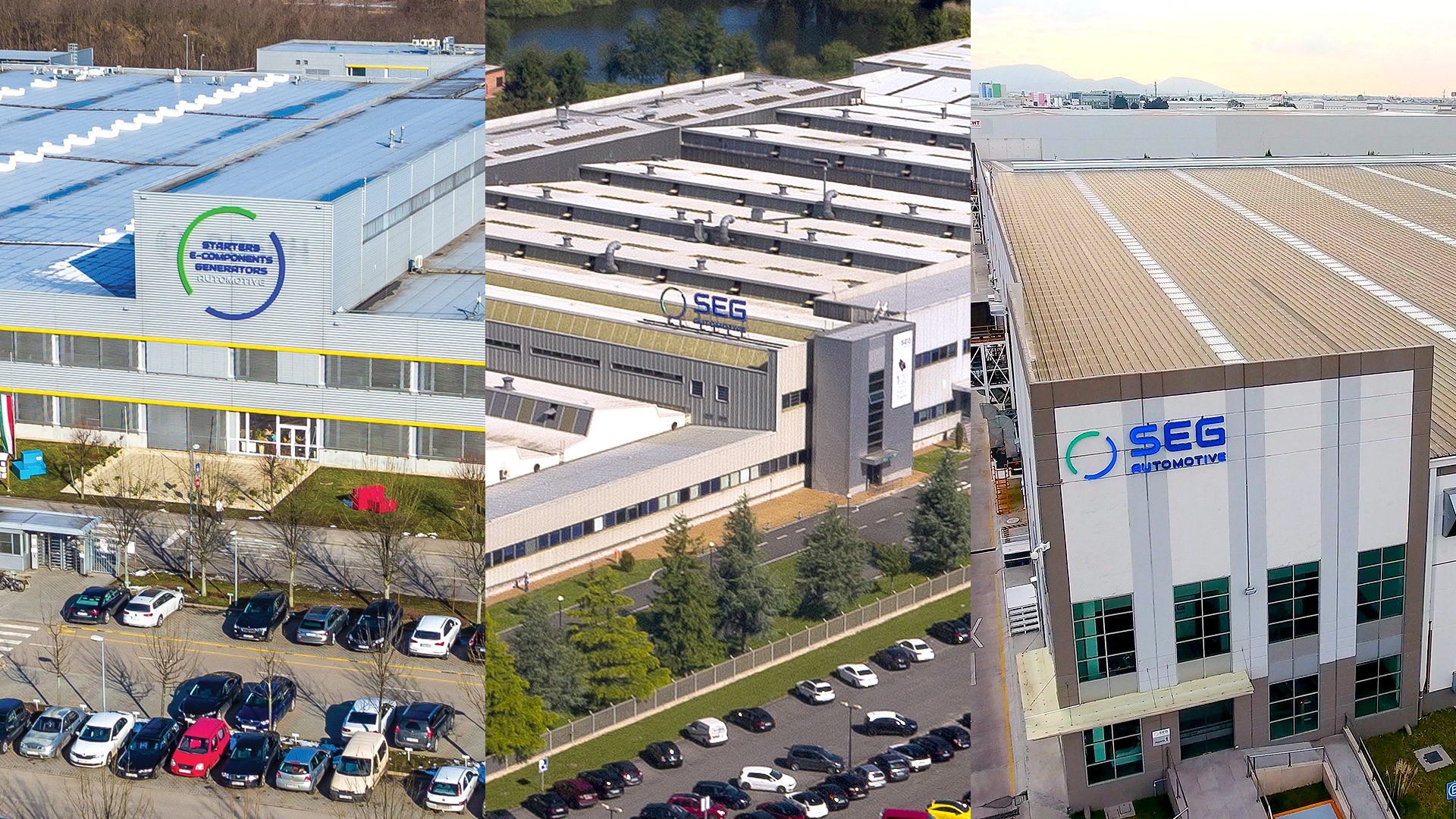
Already coping with the aftermath of Hurricanes Irma and Harvey, the crisis response team was nevertheless able to move fast when it received email alerts and a detailed report about the earthquake. Last year, for example, a magnitude 7.1 earthquake in central Mexico caused hundreds of deaths and impacted many GM supplier operations in the area. Key internal customer Bill Prince, one of GM’s supply chain crisis managers, can attest that the risk-notification system gives the automaker more response time. For example, if a fire breaks out at a supplier plant and a local news station covers it, Rossi and team will hear about it in near real time. In essence, the system listens to a wide variety of information sources around the world and generates alerts when adverse events crop up. “It has allowed us to get all relevant information in one spot and run reports quickly.” “We’ve been able to integrate data feeds directly into our GIS tool,” he says. GM also partners with several companies to obtain data from news sources and providers of critical weather information. In those scenarios, the SCRM team works with the suppliers directly to make sure they’re doing everything they can to manage risk, and to establish a clear expectation of what their crisis reporting to GM should look like. Some suppliers shield the identity of their supply base, he notes, making them reluctant to provide details. We set a new expectation by putting a process in place to receive this information from our suppliers during the sourcing process,” he says.
#GM SUPPLIER AND XPLAN GROUPS MANUAL#
“It took a big manual effort of us reaching out individually to our tier 1 suppliers. It proved much more difficult to map the sub-tiers, the suppliers that ship to GM’s tier 1 suppliers and their suppliers. “We have all the location information and data for our tier 1 supply base-the suppliers that ship directly to GM,” Rossi says. Mapping GM’s supply base into the GIS (see image below) required a substantial upfront effort as well as ongoing maintenance, especially when it came to the tier 2 and tier 3 suppliers. He and his colleagues investigated 700 events (and took action on one-third of those) in 2017, the first year the system was in place. By the time you know about them, you’re already in recovery mode,” Rossi says. “The most important thing is being able to respond and recover quickly when disruptive events occur around the globe-events like earthquakes, factory fires. If it looks like a part shortage could threaten production, Rossi’s colleagues in crisis management can activate their contingency plans much sooner than was possible when they manually collected data about adverse events.

When an event such as a factory fire or a storm occurs, the system enables the team to focus on a specific part and trace it from its source to its destination plant and vehicle program. To do that, Rossi relied on a geographic information system (GIS) that maps the interconnections among GM’s thousands of tier 1, tier 2, and tier 3 suppliers. When problems arise, the faster the SCRM team can get information to GM’s global crisis managers, the quicker the company can resolve those problems before customers are affected. GM’s production is exposed to a broad range of disturbances-from political uprisings and weather events to labor disruptions and supply shortages.
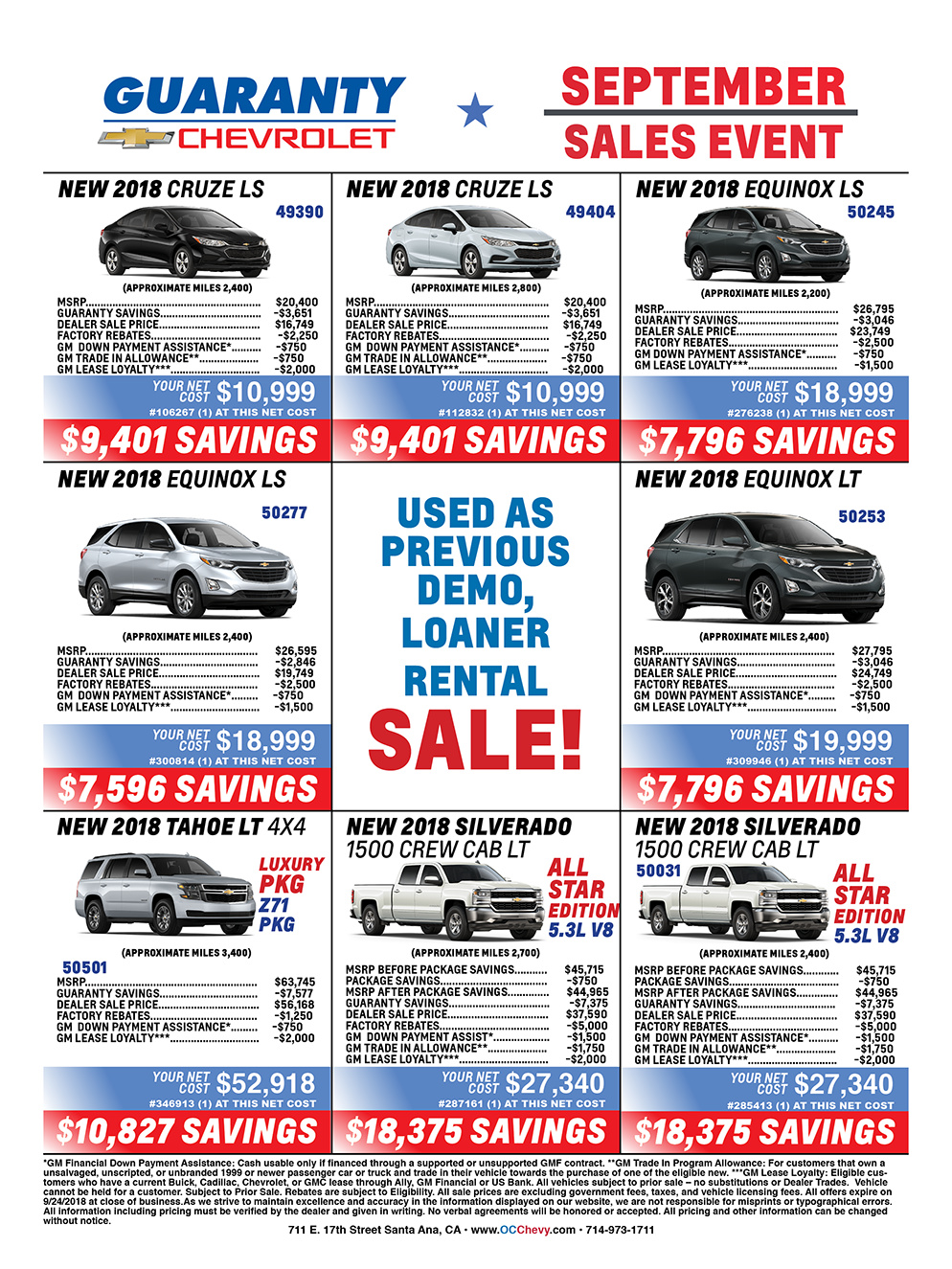
But as with any automaker, so much can go wrong. Suffice to say, GM’s worldwide production operation is a well-oiled machine. GM produces more than 10 million vehicles a year, sources more than 100,000 unique parts from 5,500 supplier sites worldwide, and sells its cars in more than 100 countries. Just ask Paul Rossi, currently a member of the strategic risk management team at General Motors, and formerly the company’s supply chain risk management (SCRM) lead. But if you’re in charge of monitoring global supply chain risks for one of the world’s largest automakers, there’s a lot to keep you up at night. Everyone has trouble sleeping from time to time.
